Brass Forged Parts: Benefits and Insights into the Forging Process
Brass forged parts are high-strength components manufactured through the forging process, which involves shaping brass under extreme pressure.
This technique produces parts with superior mechanical properties, precision, and durability, making them essential in industries such as plumbing, automotive, aerospace, and electrical systems.
Understanding what brass forged parts are and the forging process itself highlights why this method is a preferred manufacturing choice.
What Are Brass Forged Parts?
Brass forged parts are components crafted by compressing brass into specific shapes using high-pressure forging techniques. These parts stand out for their:
- High Strength: The forging process enhances the structural integrity of the material.
- Precision: Allows for exact dimensions and tight tolerances.
- Corrosion Resistance: Retains the natural durability of brass, making it ideal for harsh environments.
- Wide Applications: Used in plumbing, automotive, aerospace, and other industries requiring robust and reliable components.
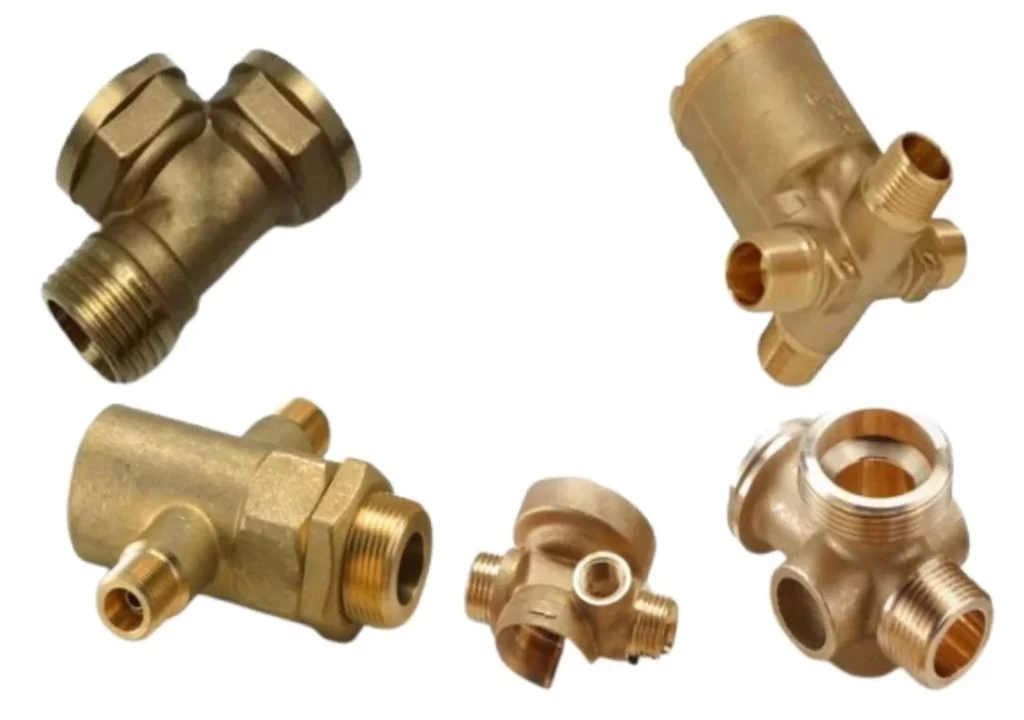
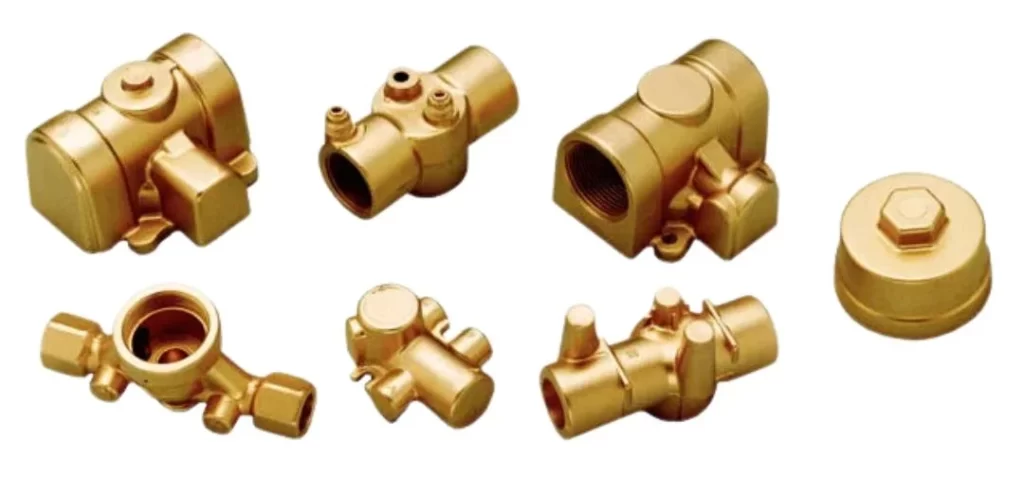
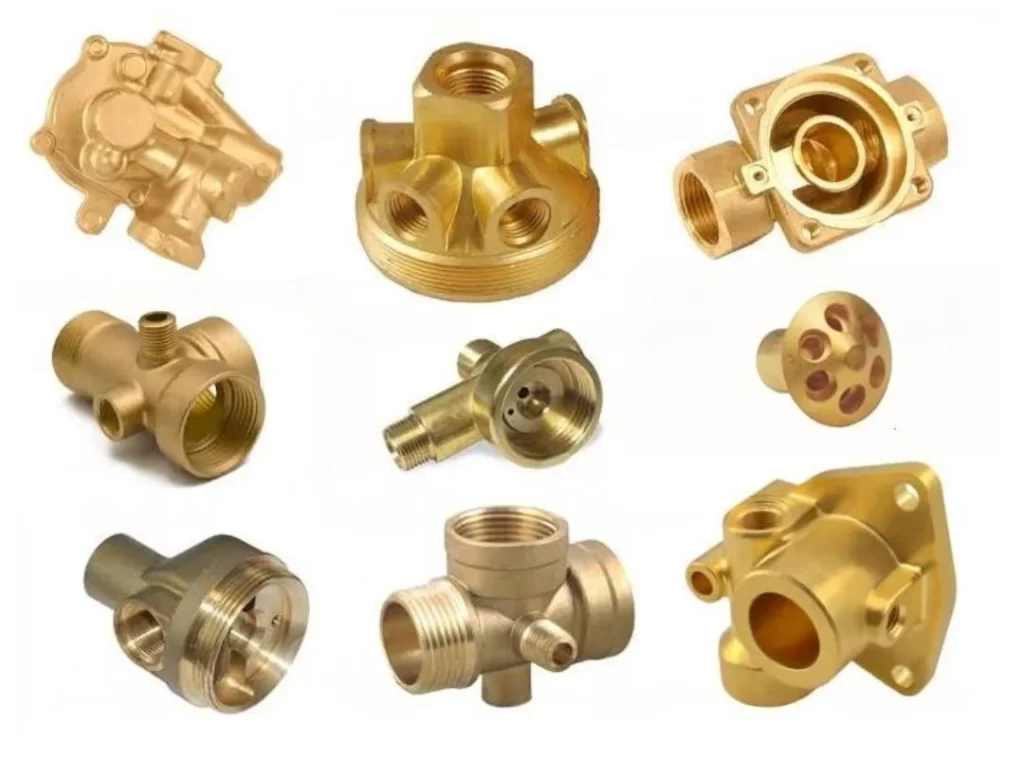
What Is the Forging Process?
Forging is a manufacturing method that involves applying compressive force to a heated or cold brass billet to shape it into the desired form. The process improves the material’s grain structure and mechanical properties, making it stronger and more durable.
Steps in the Forging Process
Material Selection : High-quality brass alloys are chosen based on the specific application and performance requirements.
Heating the Brass billet (Optional) : The brass is heated to increase its malleability for hot forging. Cold forging skips this step and uses brass at room temperature.
Shaping the Brass :
- The heated or cold billet is placed into a die, which gives the part its final shape.
- High-pressure force is applied using a hammer or press.
Trimming & Finishing :
- Excess material, known as flash, is trimmed off to refine the part’s edges.
- Finishing processes, such as polishing or coating, may be applied to enhance the part’s appearance and durability.
Quality Inspection :
- The forged parts undergo rigorous testing to ensure they meet industry standards for strength, precision, and performance.
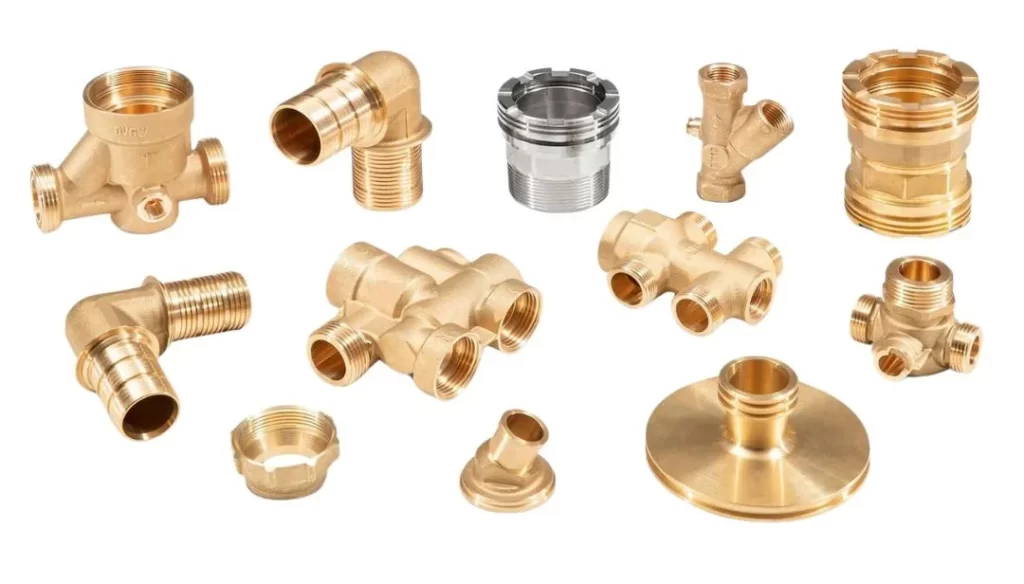
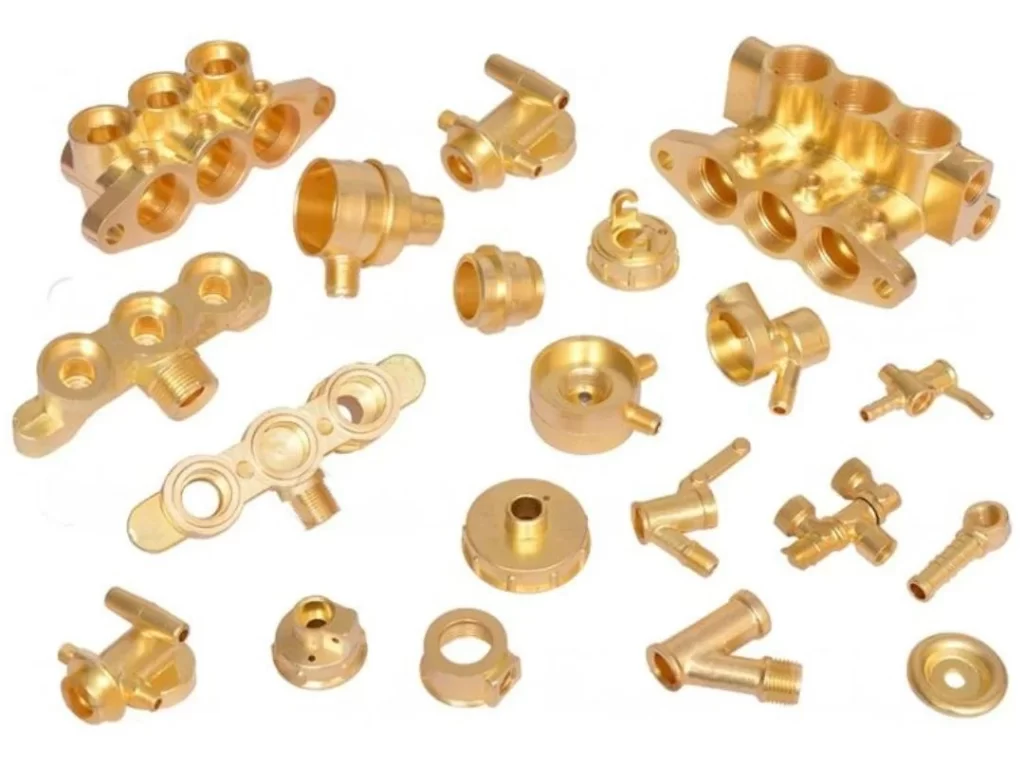
How Forging is Used in Brass Parts Manufacturing
Forging is widely used to produce a variety of brass parts due to its ability to create components with superior properties:
- Plumbing Components: Valves, fittings, and connectors that need to resist leaks and corrosion.
- Electrical Parts: Connectors, terminals, and switchgear components with high conductivity and strength.
- Automotive and Aerospace Parts: High-pressure hydraulic fittings, fuel line components, and other critical parts.
- Decorative and Architectural Hardware: Door handles, knobs, and fixtures with enhanced aesthetic appeal.
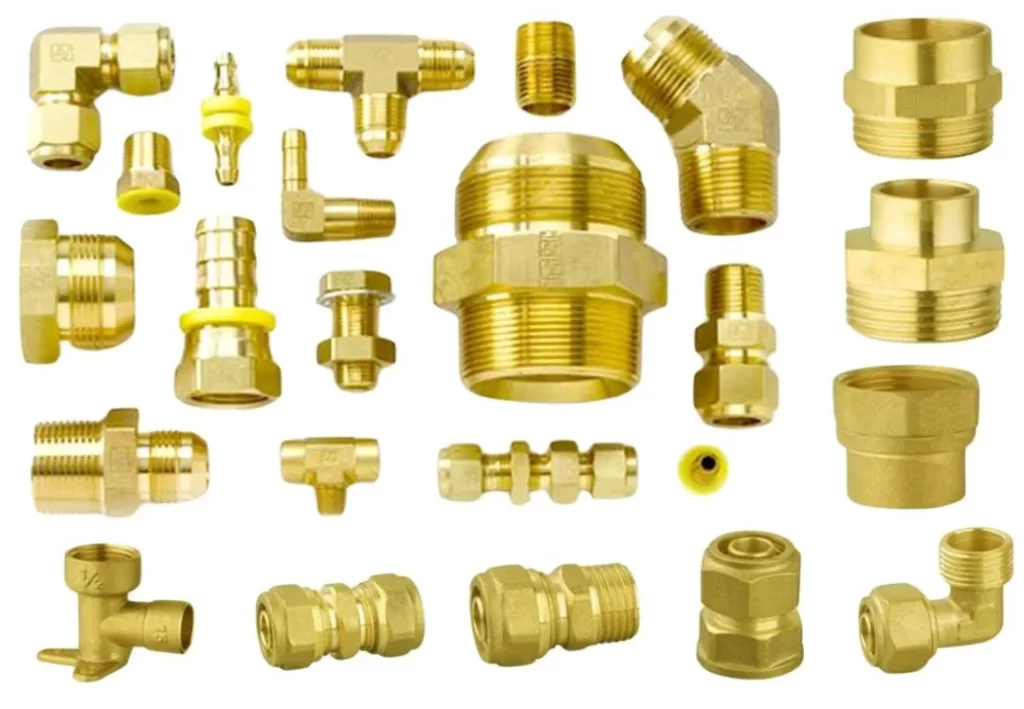
Benefits of Using the Forging Process for Brass Products
The forging process offers several advantages, making it the preferred method for manufacturing brass products:
Enhanced Strength and Durability
- The grain structure of brass aligns during forging, resulting in parts with superior tensile and impact strength.
Precision and Dimensional Accuracy
- The process ensures exact dimensions, which are critical for applications requiring tight tolerances.
Corrosion and Wear Resistance
- Forged brass retains its natural resistance to corrosion, ensuring a longer service life in harsh conditions.
Improved Aesthetic Finish
- Forged parts can be polished or coated to achieve a smooth, high-quality appearance, making them ideal for visible applications.
Cost-Effectiveness
- While forging may have a higher upfront cost compared to casting or machining, it reduces long-term maintenance and replacement expenses due to its durability.
Environmental Sustainability
- Brass is recyclable, and forging minimizes material waste, making it an eco-friendly manufacturing option.
Safety in Critical Applications
- Forged brass parts are free of internal voids or defects, ensuring reliability in applications where safety is paramount, such as in aerospace and automotive systems.
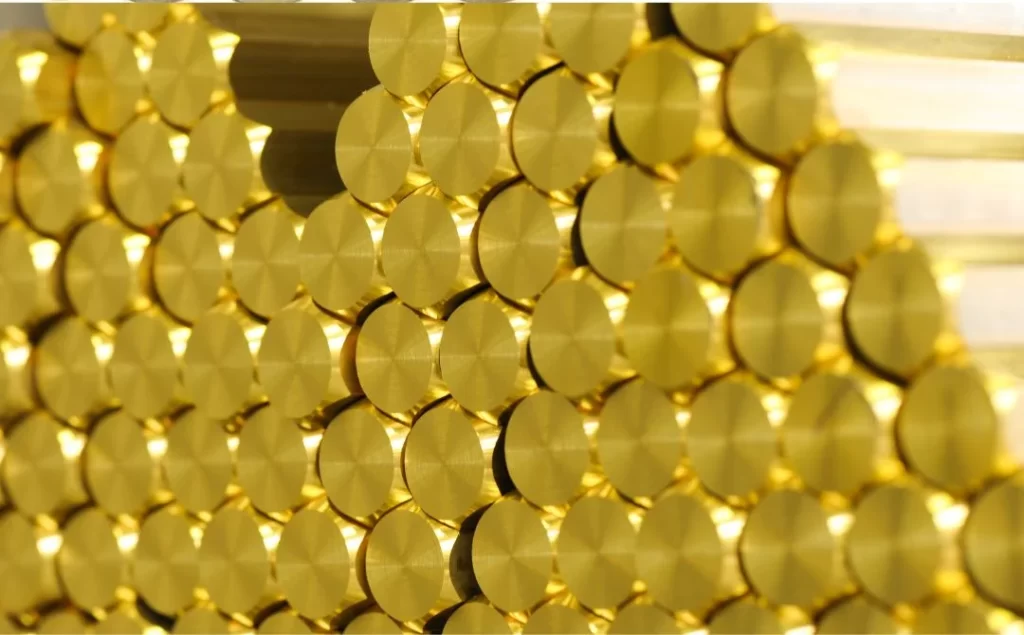
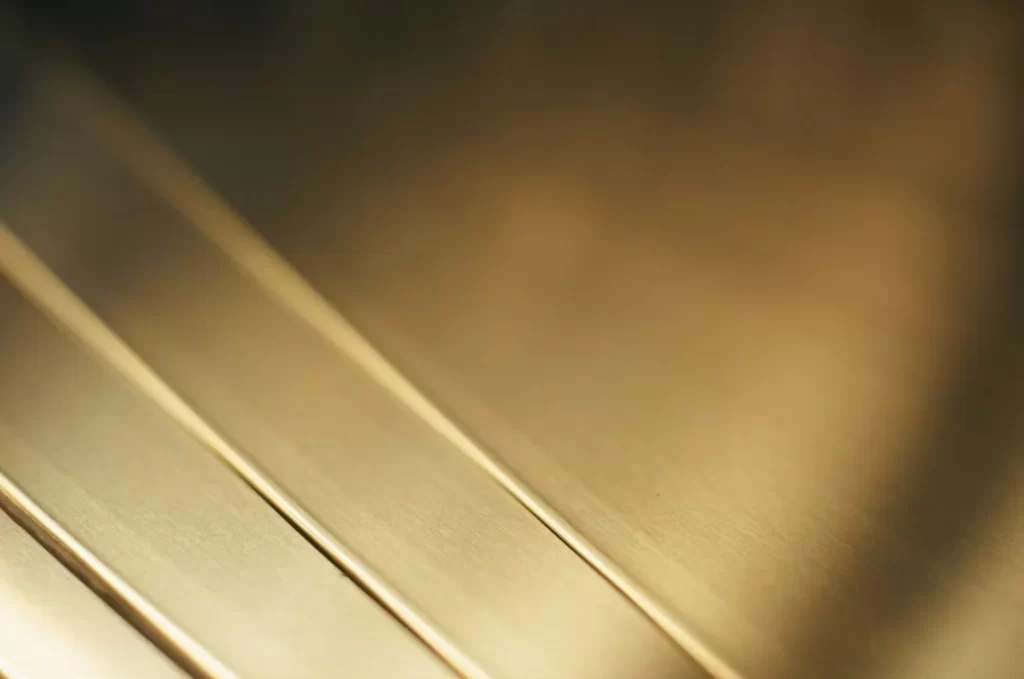
Conclusion
Brass forged parts are a cornerstone of high-performance applications, offering unmatched strength, precision, and corrosion resistance.
The forging process, which enhances the grain structure and properties of brass, ensures the production of reliable and durable components.
By choosing forged brass parts, industries benefit from superior mechanical properties, longer service life, and reduced maintenance costs.
Whether for plumbing, automotive, aerospace, or decorative purposes, the forging process delivers unparalleled quality, making it a trusted method for brass parts manufacturing in modern industries.